|
|
- Description
- Features
- Benefits
|
|
|
Product Specifications |
|
- Mechanical
- Electrical for Low Volt Model
- Electrical for High Volt Model
|
Dimensions |
4.75"h x 2.0"w x 11.0"l (120.6mm x 50.8mm x 279.4mm) |
Mounting Dimensions |
1.25" wide x 10.25" long, four 0.25" diameter hole |
Weight |
5 lbs. (2.27kg) |
Operating Temperature |
-10°F to +140°F (-23°C to +60°C) |
|
|
Power Input |
120 vdc ±10% @ 5.0 amps |
Armature Current |
0.5 - 6.5 amps |
Armature Voltage |
0 - 24 vdc |
Encoder Input |
5 or 15 vdc 100 lines/rev max frequency 25.0khz |
Foward Input |
24 vdc @ 20ma (Active High) |
Reverse Input |
24 vdc @ 20ma (Active High) |
Speed Reference Inputs |
0-10 vdc @ 0.1 ma |
|
|
Power Input |
120 vdc ±10% @ 5.0 amps |
Armature Current |
0.5 - 3.0 amps |
Armature Voltage |
0 - 100 vdc |
Field Voltage |
110 vdc nominal |
Encoder Input |
5 or 15 vdc 100 lines/rev max frequency 25.0khz |
Foward Input |
24 vdc @ 20ma (Active High) |
Reverse Input |
24 vdc @ 20ma (Active High) |
Speed Reference Inputs |
0-10 vdc @ 0.1 ma |
|
|
|
|
|
|
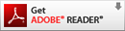 |
Note - All documents are in an Adobe PDF file format. |
|
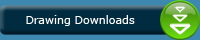 |
Press to enter download area for Autocad DXF drawing format. |
|
|